Para aumentar la productividad de la maquinaria en nuestra industria es importante llevar a cabo una serie de actividades de manera asidua, como su revisión, limpieza, o mantenimiento. Sin embargo, existe una manera de aumentar la eficiencia lo máximo posible, y esto se consigue al adquirir datos de nuestra maquinaria industrial. De esta manera podremos conocer a fondo su funcionamiento e implementar de manera concisa diferentes soluciones.
¿Cómo podemos adquirir estos datos de la maquinaria industrial?
A medida que nos adentramos en la Industria 4.0, vamos siendo más conscientes de la importancia que tienen los datos para el éxito de cualquier ámbito. La captación de datos de alta calidad no sólo ayuda a crear ideas que sirvan para mejorar la productividad y rentabilidad; también es un primer paso esencial hacia la industria manufacturera de alta tecnología que cada vez gana más y más peso en nuestra economía.
Los sistemas de adquisición de datos de la producción adquieren información de múltiples fuentes, la analizan y finalmente emiten los resultados. Los datos pueden proceder de detectores de temperatura, transductores de presión, sensores de proximidad, o cualquier otra fuente de tensión, corriente o resistencia.
Posteriormente, el hardware, software, o la combinación de ellos, analizan estos datos. Así, estas señales de proceso y medición que suelen ser analógicas, se convierten en digitales.
Todos los sistemas de adquisición de datos suelen contar con 3 elementos principales: el sensor, el acondicionamiento de la señal, y el convertidor analógico-digital. Además, los sistemas suelen diferenciarse entre 2 tipos, los digitales y los analógicos. Por lo general, con un sistema digital obtenemos más ventajas, ya que tienen un procesamiento y una transmisión más fácil y rápida, fácil visualización, se requiere menor espacio de almacenamiento, y ofrecen mayor precisión.
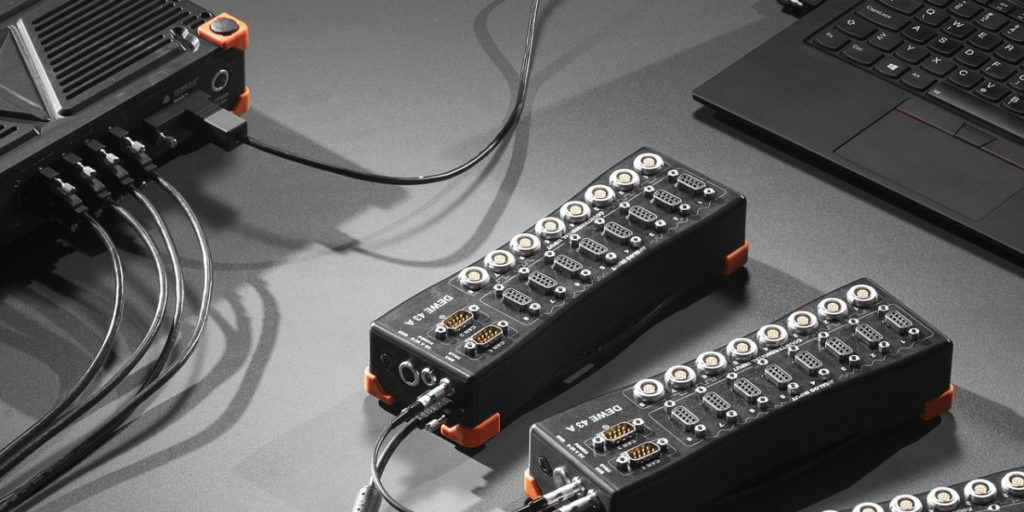
Tecnologías para la extracción de datos
Existen diferentes tecnologías para llevar a cabo la extracción de datos de la maquinaria. A continuación vamos a ir viendo brevemente cada una de ellas y sus principales beneficios.
1. Datalogging
El Datalogging permite registrar los datos de los sensores (internos y externos) a los que está conectado el datalogger. Casi todos los dataloggers están basados en microcontroladores. Algunos de ellos están provistos de pantallas LCD, tienen capacidad de ser programados, o de gestionar la actividad remota. Suelen ser dispositivos con funciones muy concretas, y aunque llevan mucho tiempo en el mercado, cada vez se ven más reemplazados por dispositivos de red con más funcionabilidades que incorporan la opción de Datalogging.
Sus ventajas es que son robustos, sencillos, y no intervienen en el control de la aplicación. Sin embargo, su funcionamiento es limitado y no cuentan con gestión remota.
2. Telecontrol remoto
El Telecontrol remoto utiliza protocolos sobre IP para brindar conectividad entre dispositivos que se encuentran en diferentes redes. Se apoya en 3 grupos de servicios básicos: servicios de autentificación de usuarios, tunelización IP y funciones de enrutamiento de red.
Su principal función es permitir a usuarios o sistemas remotos conectarse entre sí o a diferentes dispositivos, como si estuvieran en el mismo segmento de red. El fin es el de monitorizar, controlar y mantener los dispositivos desplegados.
Sus beneficios son el ahorro en costes de mantenimiento, servicios de ciberseguridad que ofrecen cada vez una conexión más segura, y su compatibilidad con múltiples sistemas operativos. Sin embargo, se limita a la gestión de sesiones remotas, no actúa de forma autónoma (depende de la supervisión del operador), y carece de una base de datos.
3. Edge Computing
El término Edge Computing se refiere al tratamiento de datos obtenidos en un sensor o dispositivo que se encuentra muy próximo a él (básicamente, en su mismo segmento de red).
Algunos equipos están dotados de características técnicas que les permiten actuar, por lo que el resultado de sus cálculos puede derivar en acciones relacionadas (o no) con otros elementos inteligentes.
El Edge Computing tiene una mayor autonomía en los dispositivos, una mayor latencia en la obtención de datos, menor requerimiento de ancho de banda, menores constes y consumo eléctrico, menor impacto en el proceso en caso de fallos, y aporta una mayor seguridad.
El único contra que podemos encontrar es que tiene una arquitectura más compleja de supervisar, mantener y controlar, debido al múltiple número de dispositivos.
4. Cloud Computing
Son centros de cómputo conectados a Internet, que reciben y procesan gran cantidad de información para tomar decisiones y obtener conclusiones.
Es importante destacar que el Cloud Computing por sí solo no aporta una solución. Por el contrario, requiere de sensores/actuadores para poder recibir información y actuar sobre el proceso, así como mostrar información al usuario.
Su alcance es global, y sus características le otorgan agilidad, efectividad en costes, escalabilidad, elasticidad, fácil mantenimiento y capacidad de operación con múltiples dispositivos y usuarios. Por otro lado, aumenta la exposición a ciberataques, aumenta la latencia, disminuye la autonomía de los dispositivos, es incompatible con sistemas autónomos, requiere un mayor ancho de banda, consume más energía, y en caso de fallos, el impacto afecta a gran parte del proceso.
¿Qué datos de la maquinaria industrial nos resulta beneficioso adquirir?
Pues bien, una vez tenemos claras las distintas tecnologías y formas en las que se pueden adquirir los datos de la maquinaria, la pregunta es: ¿qué datos adquirir?
Existen multitud de factores que influyen en los procesos de producción, y tener una amplia variedad de muchas y diversas operaciones suele resultar beneficioso. Sin embargo, existen una serie de datos específicos que suelen incluirse más habitualmente en la recopilación, y son los siguientes:
- Estado de los equipos: utilizando sensores, se puede recabar información detallada sobre los equipos. La recopilación de datos permite ver cuándo está en funcionamiento un equipo, su eficiencia y mucho más.
- Gestión de líneas: la gestión de líneas implica muchos factores diferentes, y las tecnologías de recopilación de datos pueden ayudar a mantenerlos todos bajo control. Obtener una visión más clara de nuestra línea de producción puede ayudarnos a mejorar su eficiencia.
- Datos energéticos: la recopilación de datos en tiempo real sobre el consumo de energía nos ayuda a incrementar la eficiencia energética, reducir los costes y lograr una producción más sostenible.
- Tiempos de ciclo de pedidos: si realizamos un seguimiento de parámetros relacionado con el tiempo de ciclo de un pedido, podremos tomar medidas para mejorar el proceso. Así podemos mejorar la satisfacción del cliente, aumentar el número de pedidos completados e incrementar los beneficios.
- Tarifas y plazos de envío: supervisar y analizar las tarifas y los plazos de envío nos permite realizar estimaciones más precisas sobre los envíos, reducir los costes de los mismos y entregar pedidos más rápidamente.
- Precisión de entrega: es un factor muy importante para la satisfacción del cliente. Supervisar los parámetros relacionados con este factor, nos permite identificar las posibles causas de las entregas de pedidos incorrectas y corregirlas.
De esta manera, mejoraremos la eficiencia y productividad de nuestros procesos productivos.
0 comentarios