I-IoT Platform, Smart Environment in Industry
I-IoT Platform, responsible for creating new levels of visibility by connecting sensors, machines, and other devices in a unified environment.
Project data
CLIENT
Manufacturing company of construction materials
SECTOR
Industry 4.0
GEOGRAPHY
National
YEAR
2019
The concept
The project addresses the client’s need for a modern, efficient, and secure tool for collecting, managing, and processing data from industrial machinery in a multi-vendor environment, with control and monitoring information silos, making it challenging to obtain a comprehensive view of the manufacturing process for each production line.
What is the purpose of the I-IoT Platform project?
The main challenge of the project is to collect, normalize, and manage the exchange of data between different areas of the manufacturing plant, each governed by a specific and independent control system within a production line that has evolved through the acquisition of new machinery.
The ultimate goal is the digital transformation of production lines to the Industry 4.0 paradigm, interconnecting existing machinery through different communication protocols, processing and treating data to achieve a holistic view of the plant.
The purpose is to connect all operational processes and allow the aggregation of information from other areas of the business (human resources, raw material stock, …) to perform a joint treatment of all available data that aids in intelligent decision-making.
Discover the application areas of IoT and our advanced services.
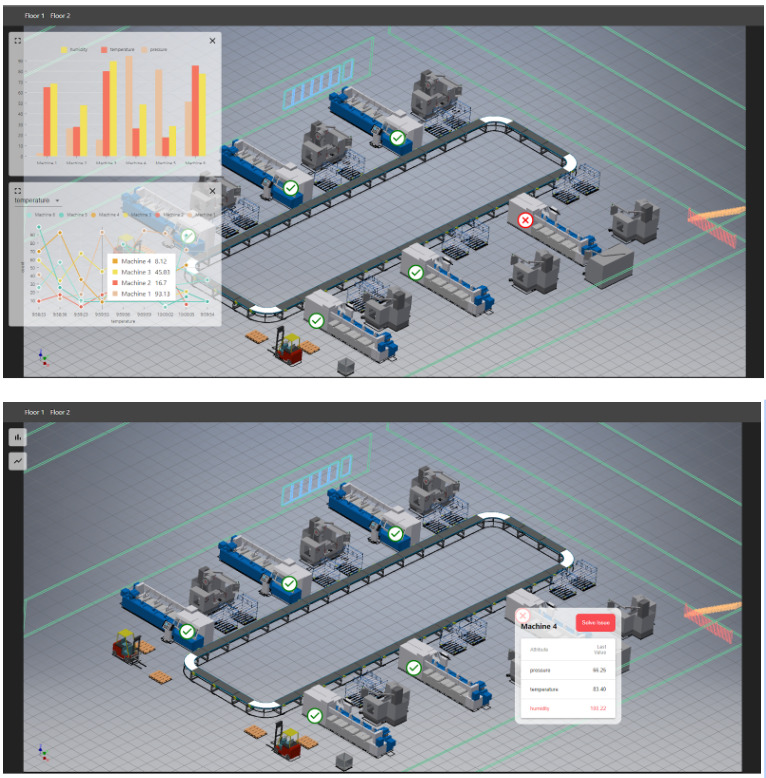
How does it work?
By using standard communication protocols such as OPC-UA and Modbus-TPC, information is gathered from each data source in the production plant for the control and monitoring of industrial machinery:
Through secure HTTPS connections, REST APIs facilitate seamless data exchange with various applications across different business areas, leveraging artificial intelligence to optimize processes.
Specific pipelines are defined for the extraction, loading, and transformation of data from databases across different business areas, incorporating machine learning techniques to enhance the accuracy and efficiency of the process.
Once normalized, the data is ready for management, processing, and visualization. To achieve this, a web interface enhanced with artificial intelligence algorithms is integrated, facilitating the representation of information through dynamic charts and diagrams.
Additionally, the generation and editing of indicators and business rules are enabled using natural language processing techniques, allowing for the triggering of automatic actions in any of the interconnected systems based on the values of the collected variables.
This synergy between data collection and artificial intelligence enhances decision-making and operational efficiency in the production plant.
What problems does this solution solve?
The main advantages provided by the deployed Platform are:
- Possibility of monitoring and control of multi-manufacturer industrial machinery from a single environment.
- Coordinated management of the entire production line and automation of processes that were initially not interconnected: optimization of the manufacturing process.
- Unified management of alarms and events: minimization of downtime.
- Aggregation of valuable information by integrating operational data with data from other business areas: support for strategic decision-making.
- Ease of integration of future sources of information into the platform.
Download this project as a PDF
In the following download button:
Discover the application areas of IoT and our advanced services
Other noteworthy projects
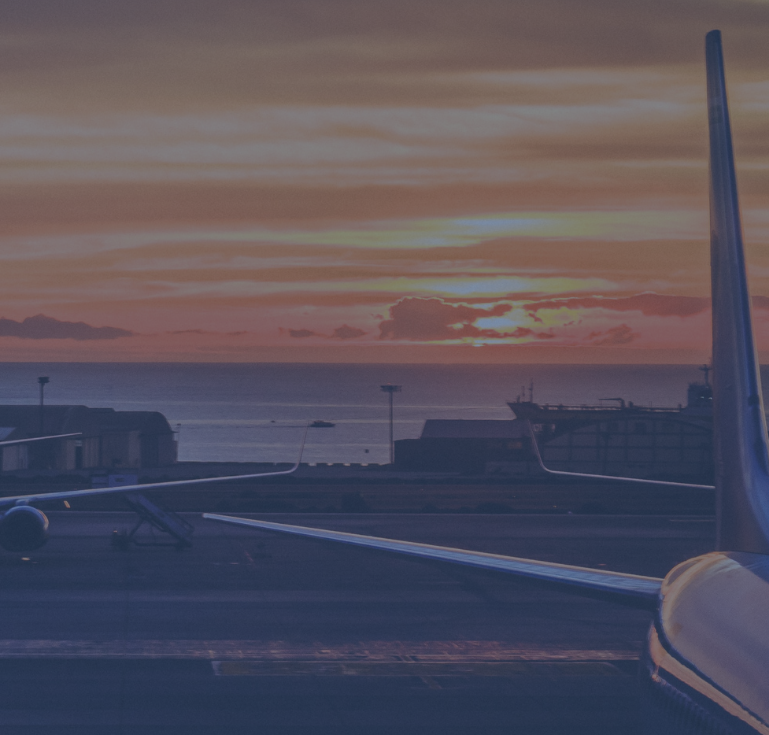
DTN and its digital transformation process

Smart Trucks, firefighter fleet management
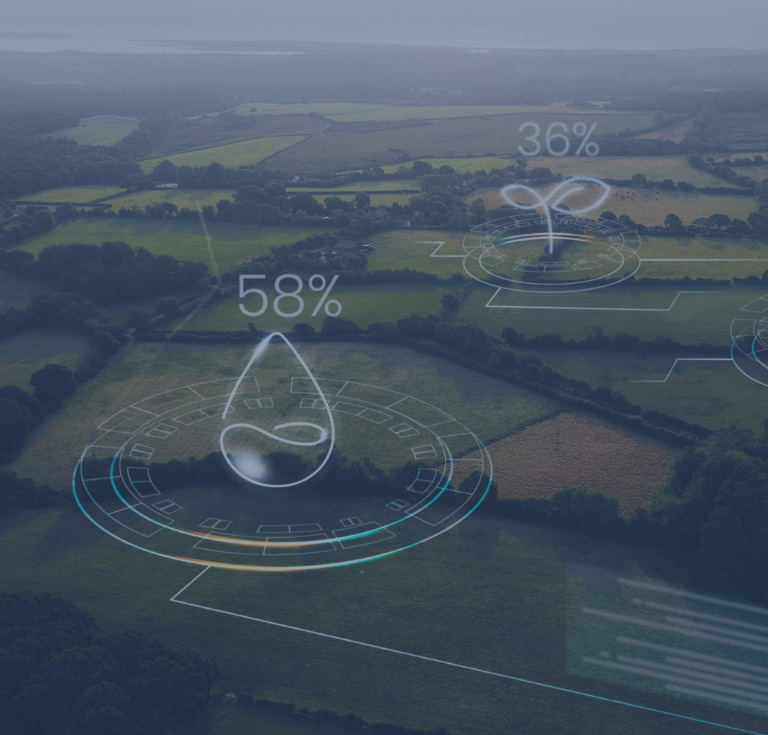
Secmotic participates in the AgrarIA project
Get Smart

Calle Factores 2, 41015 Seville
Phone: +34 618 72 13 58
Email: info@secmotic.com
INNOVATION HUB

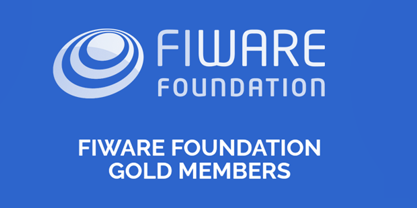

