Smart QA | Management of large volumes of data through Artificial Intelligence
This project is based on the creation from scratch of an artificial intelligence system for early detection of manufacturing defects in QA (quality control)
Project data
CLIENT
Aerospace industry
SECTOR
Industry 4.0
GEOGRAPHY
National
YEAR
2019
The concept
Early and effective detection of manufacturing defects is an essential component to ensure customer satisfaction and operational efficiency.
In this context, this project is born, an initiative that merges the capabilities of Artificial Intelligence with the precision of multivariable analysis and industrial data processing.
What goal has this project achieved?
How does it work?
The system is based on the integration of various technological components and data analysis methodologies to achieve its functionality. The process unfolds in the following stages:
- Data Acquisition: Data from industrial sensors and Quality Control (QA) reports are collected and stored.
- Data Preprocessing and Transformation: Data engineering is applied to clean, normalize, and structure the data in a format suitable for analysis.
- Multivariable Analysis: Statistical techniques and multivariable analysis algorithms are employed to identify correlations and patterns in the data. This helps understand interactions between variables and detect subtle anomalies.
- Pattern and Defect Detection: Using machine learning algorithms, AI identifies anomalous patterns that may indicate potential manufacturing defects. These patterns might be imperceptible to conventional control systems.
- Prediction of Anomalous Values: The system can predict anomalous values and unusual behaviors based on trends identified in historical and real-time data.
What problems does this solution solve?
- Early Defect Detection: The solution addresses one of the most critical challenges in industrial production by enabling the early identification of potential defects, reducing the number of defective products reaching the market, and minimizing associated costs.
- Optimization of Quality Control Processes: By automating a significant portion of the defect detection process, the system allows a more efficient allocation of human resources to higher-value tasks in quality control.
- Cost and Waste Reduction: By predicting and preventing manufacturing defects, costs associated with rework, repairs, and returns of defective products are reduced.
- Improved Decision-Making: AI provides detailed information about production and quality patterns, enabling more informed and strategic decision-making.
- Increased Competitiveness: By improving product quality and production process efficiency, the solution contributes to enhancing the brand image and customer satisfaction, thereby increasing competitiveness in the market.
In summary, the project aims to apply cutting-edge Artificial Intelligence and data analysis technologies to revolutionize the Quality Control process, enabling early detection of manufacturing defects and generating a positive impact on the efficiency, quality, and profitability of industrial operations.
Other projects of interest
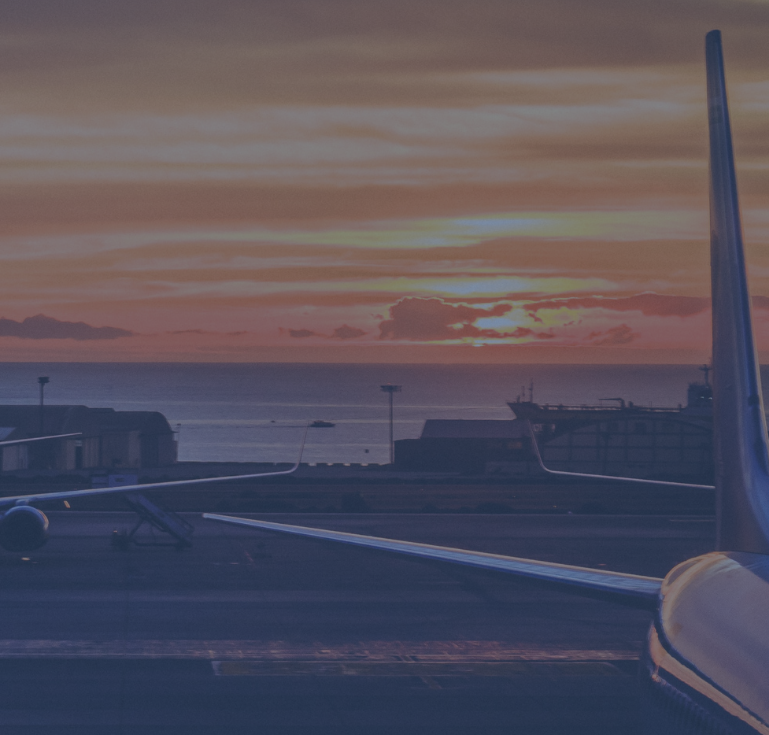
DTN and its process of digital transformation

Smart Trucks, fire fleet management
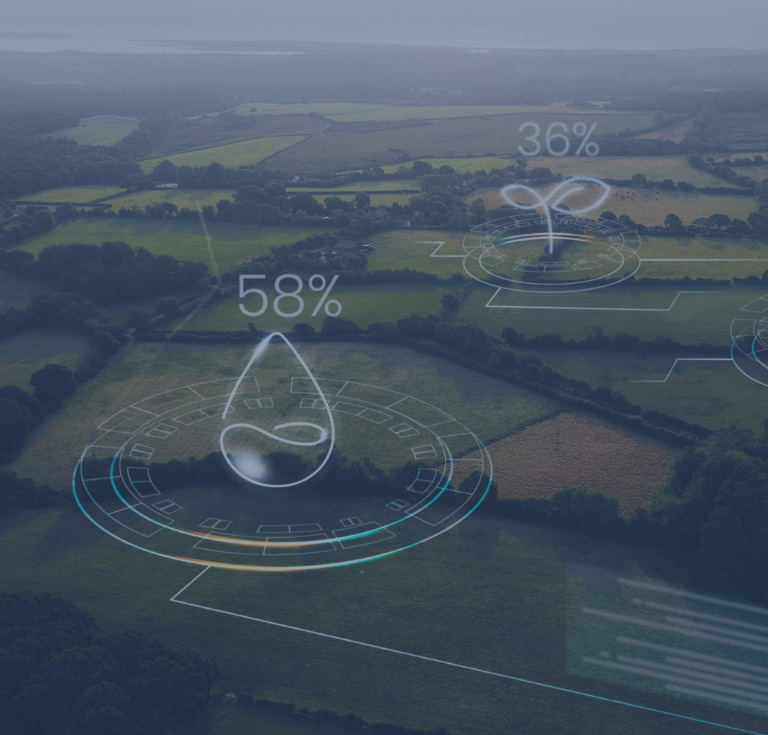
Secmotic participes in the AgrarIA project
Get Smart

Calle Factores 2, 41015 Seville
Phone: +34 618 72 13 58
Email: info@secmotic.com
INNOVATION HUB

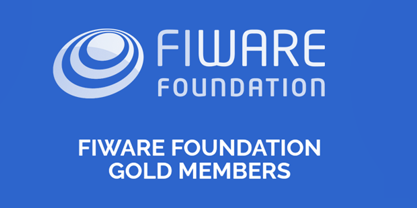

